Products
Solutions
Resources
9977 N 90th Street, Suite 250 Scottsdale, AZ 85258 | 1-800-637-7496
© 2024 InEight, Inc. All Rights Reserved | Privacy Statement | Terms of Service | Cookie Policy | Do not sell/share my information
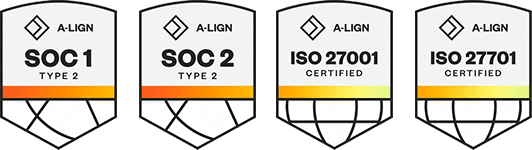
As one of the applications within the InEight portfolio of products, InEight Plan is a tool for engineers and superintendents to plan work and track quantities during the execution of their project.
Plan is organized into two modules:
Plan Modules |
|
---|---|
Work Packaging |
Creating and managing work packages. |
Quantity Tracking |
Creating and managing components and claiming schemes. Claiming completed quantities. |
This course focuses on the Quantity Tracking module of InEight Plan.
Plan Quantity Tracking uses some key terminology to describe how the work is broken down for tracking.
The table below defines each of the key terms you should know.
Term |
Definition |
Managed In.. |
---|---|---|
CBS (Cost Breakdown Structure) |
Hierarchy of budgeted work activities (cost items) in a project. |
|
WBS (Work Breakdown Structure) |
Code assigned to terminal cost items for tracking purposes. |
|
ACS (Account Code Structure) |
Standard Classification code used for benchmarking similar types of work between projects. |
|
Component |
Item or element of work used for maintaining quantities. |
|
Claiming Scheme |
A method used for tracking component progress via use of sublevel tasks (steps). |
|
The relationship between these terms is shown in the following diagram:
You are a structural steel field engineer responsible for accurately tracking installation progress for a steel structure project. See image below. The structural steel cost item is measured in tons, but steel is installed by piecemark, and it needs to be tracked as such. There are multiple steps to structural steel installation that are all coded to the same cost code, and you need a way to track completion of the different steps as well. You also want to easily communicate to your foreman what he needs to accomplish each day to stay on schedule and on budget.
The image above depicts a layout for a steel structure project. The project consists of erecting 30 separate steel structures on opposite sides of a road. Each structure or module has been assigned a number 1-30.
Within the InEight Control application, cost items are identified by a WBS Phase Code (commonly referred to as simply the WBS). A unique WBS is assigned to each cost item in the CBS, including superior and terminal items. The WBS codes can be set up to be automatically assigned or manually input.
In InEight Plan, the Quantity Tracking module allows you to break down quantities into more manageable tasks to track and claim against. You accomplish this by breaking down your WBS Phase Code quantity into smaller pieces called components.
Referring to the scenario above, your project has an ‘Erect Steel – Light’ cost item with a WBS Phase Code of 1005, as seen in the CBS register of the Control application.
For tracking purposes, in the Quantity Tracking module of Plan, you can break down the ‘Erect Steel – Light’ WBS Phase Code into distinct components by structural steel piecemark:
Each component has a measured quantity:
Component |
Quantity |
---|---|
A14: Beam |
0.44 Tons |
F16: Beam |
0.45 Tons |
C23: Cross Brace |
0.26 Tons |
The sum of the quantities for each component adds up to the total quantity for the assigned WBS.
Components can have a myriad of attributes assigned to them to help organize and store pertinent information that can be used for filtering and reporting. These include but are not limited to:
Discipline
Area
System
Customizable Attributes
In Lesson 4 – Component Management, you will learn how to create components either through import from an Excel template or by creating them manually.
Claiming schemes break components down further, to a sequence of steps, so that foremen can track the individual steps as the installation of the component progresses. Each step has a weighted rule of credit, based on percentages, that will progress the overall component.
Claiming schemes can be assigned at either the component, WBS, or Account Code level. If a claiming scheme is assigned at the WBS level, then every component that is assigned to that WBS will automatically inherit the same claiming scheme.
The level at which claiming schemes will be assigned (Account Code, WBS, or component) will typically be dictated during project initiation in the project settings. See Lesson 3 – Claiming Schemes for more details on assigning claiming schemes.
For example, you may break down the ‘A14: Beam’ component into the following steps for tracking in the field:
Claiming Scheme for ‘A14: Beam’ Component |
||
---|---|---|
Step |
Description |
Percentage |
Step 1 |
Shakeout/Transport |
15% |
Step 2 |
Erect/Bolt Up |
45% |
Step 3 |
Final Torque |
30% |
Step 4 |
QC Verification |
10% |
The diagram below shows how the claiming scheme relates to the component, WBS Phase Code, and Account Code.
In the field, the foreman can indicate when each step has been completed for a specific component. By indicating Step 1: Shakeout/ Transport is complete for ‘A14: Beam’, this will claim the component is 15% completed. After syncing this information to InEight Control, 15% of the quantity for A14: Beam will be added to the total quantity complete for that WBS code which will drive the earned value.
The diagram below shows the flow of quantity claiming through components and claiming schemes.
The quantities tracked at the component level will “roll up” to the assigned WBS Phase Code and be available for progress analysis and forecasting in the Control application. Learn more about syncing in the Control Knowledge Library.
In this example, the quantities claimed for steel components roll up to the ‘Erect Steel – Light’ WBS item, which then gets sent to Control upon request.
Additional Information
9977 N 90th Street, Suite 250 Scottsdale, AZ 85258 | 1-800-637-7496
© 2024 InEight, Inc. All Rights Reserved | Privacy Statement | Terms of Service | Cookie Policy | Do not sell/share my information