Products
Solutions
Resources
9977 N 90th Street, Suite 250 Scottsdale, AZ 85258 | 1-800-637-7496
© 2024 InEight, Inc. All Rights Reserved | Privacy Statement | Terms of Service | Cookie Policy | Do not sell/share my information
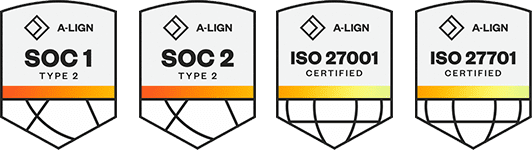
InEight Estimate is a multi-user cost estimating tool, which provides organizations the ability to accurately estimate direct and indirect cost, collect and compare contractor and supplier quotes, analyze alternate scenarios, and track all changes, as well as compare estimate revisions. Cost estimates are developed within a hierarchal structure called the Cost Breakdown Structure, where a parent-child relationship allows for the rollup of detailed cost to summary level cost items. Only the lowest level cost items within the structure, which InEight refers to as terminal items, require estimator's input.
All higher level items are simply a summation of the rows beneath them. A single cost item can be populated via three different cost sources: Plug , Detail, or Quote. The Plug cost source allows users to directly input an estimated cost. The Detail cost source employs resources such as labor crews, materials and equipment, with production rates to generate a total cost based on takeoff quantities.
The Quote cost source carries pricing submitted by a selected supplier or contractor. All cost sources can be populated, but only one will contribute to the total cost item value as determined by the cost source designation. This is very helpful when developing estimates, which may start as a Class 4 or 5 with mostly factored Plug inputs. As a project definition continues towards a Class 3 estimate, users begin to add detail via the Detail cost source.
And finally, at a Class 1 or 2 estimate, contractor provided quotes can be populated, allowing for comparison across all three inputs, and an informed selection of a preferred contractor or supplier. Predefined groups of cost items can be quickly generated using Cost Item Assemblies, which provide parameter driven estimating. Cost Item Assemblies are predefined with user required inputs, which drive calculations and reference lookup tables to populate a set of cost items. The parametric cost modeling is a powerful tool to quickly develop cost estimates simply by answering a series of questions.
Dependent cost items can also be generated based on other values in the estimate, such as man hours, total direct or indirect cost, and resource utilization. These dependent cost items will dynamically update as changes are made to estimate values, and can maintain their cost within a defined cost item, or have it allocated to specified cost items throughout the CBS. InEight Estimate maintains a master library of resource rate tables, which are employed on projects to build up detailed cost items. Hourly rates can be stored for indirect resources as well as contractor provided or historical built up labor rates.
Historical unit cost for construction equipment rentals, installed materials, installed equipment, and other unique resources can also be stored. Resource rate tables maintained in the Master Library are selected via a set of four filters in order to bring the correct rates into a new project. These customer specific filters are defined during the implementation. Some examples include the source of rates, the geographic region, the business unit, or organizational category, Much like resource filters, tagging throughout InEight Estimate allows users to add attributes to items which drives alternate views and expands reporting capabilities.
Alternate WBS structures, for example, CSI master format can be tagged to cost items in order to automatically generate a different view of your CBS to reflect a standard structure. Account codes are assigned to cost items in a similar fashion. The account codes represent a company standard coding structure, which defines like operations across all projects and estimates. The same account code is used for estimating and executing the same type of work across a company.
This enables benchmarking of past cost and a common reporting structure across estimates. Benchmarking is a powerful tool for improving the accuracy of project estimates. By employing account codes, estimators can view a graphical representation of carried rates, versus cost per unit and production rates of previous estimates and actual projects. Estimators can also quickly discover areas of risk via a benchmarking view directly in the CBS, which flags items outside the set tolerances from historical data points.
Assessment of alternate options is made significantly easier with InEight's alternate scenarios feature. This allows users to toggle on and off portions of the estimate based on the assignment of cost items to different scenarios. From technology options to different delivery methods, all can be estimated and analyzed within a single estimate file for ease of comparison and elimination of duplicate entry of commonalities. Built in integrations with Microsoft Excel, InEight Model, Scheduling software and InEight Control aim to drive efficiency.
Takeoff quantities can be updated directly from the project model and a bi-directional link to the project schedule automatically feeds schedule dates to cost items in order to project timing of expenditures and cash flow curves. Completed estimates can be pushed directly to InEight Control to create project budgets, track actual progress, and perform forecasting. New estimates can be created from scratch, from templates, or by copying all or portions of an existing estimate. Defining templates and populating the master library are keys to productive usage and realization of the many benefits InEight Estimate will bring your organization.
Additional Information
9977 N 90th Street, Suite 250 Scottsdale, AZ 85258 | 1-800-637-7496
© 2024 InEight, Inc. All Rights Reserved | Privacy Statement | Terms of Service | Cookie Policy | Do not sell/share my information